Mobile Alluvial Gold Trommel Wash Plant 2
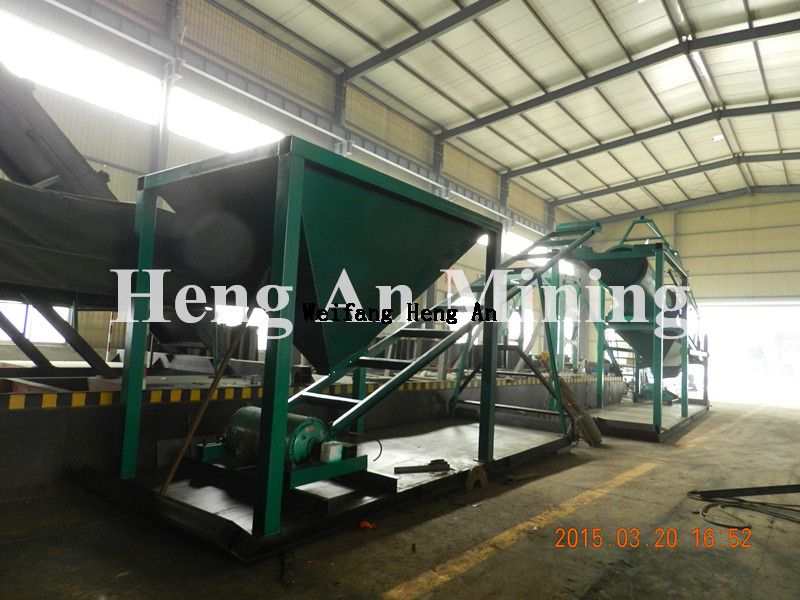
LOCATION
The alluvial mine site is located in a remote part of Papua New Guinea.
WEATHER
The mine site is subject to tropical Rainforest climate conditions with a fairly consistent climate all year.
Avg daily temperatures
|
Avg monthly rain |
Avg yearly rain |
Avg Humidity
|
|
Min |
Max |
|
||
22 deg C |
34 deg C |
200mm |
2200mm |
80% |
RIVER CONDITIONS
The local River and primary water source is the Parchee River, which is a small shallow creek, that does not dry out and often experiences flash flooding. Typically 15m wide and 0.5-1m deep in places.
ater quality may be an issue; upstream users are disturbing the water and water is muddy.
RAW MATERIAL
The raw mined material are river gravels and are quite variable but generally fall into 3 main types, one of which contains clays.
Highly sandy with very little coarse river rocks, no clays. (40%)
Lots of large coarse river rocks. (40%)
Lots of fine sticky clay material throughout gold bearing ore. (20%)
Material Particle Size Distribution
Material |
Size (mm) |
+15 |
-15 |
-10 |
-5 |
-3 |
-1 |
Total |
1 |
% |
30% |
12.5% |
12.5% |
10% |
15% |
20% |
100% |
2 |
% |
40% |
20% |
10% |
10% |
10% |
10% |
100% |
3 |
% |
20% |
15% |
15% |
15% |
15% |
20% |
100% |
Maximum top size at site is 250-400mm rocks, which are rare. Trommel needs to be protected from large rocks.
Bulk density is 1200 – 1500 kg / m3
PRODUCT GOLD CHARACTERISTICS
The current product gold is characterized by flaky gold and fine gold particles. Currently we are not finding gold nuggets. The current product particle characteristics are:
Gold Product Particle size distribution |
||
Coarse (mm) |
+1.4 |
46% |
Fine(mm) |
-1.4 |
54% |
Gold flakes >+1.4mm up to approximately 6mm (very thin and flat, not nugget)
Mobile Plant Scope Specification:
This is a mobile alluvial gold washing plant.
Mobile (skid mounted) and be towed by a bulldozer or excavator
100-140 cubic metres per hour feed rate (must average 100 cubic metres / hour)
Can operate 20 hours / day
Diesel engines to be Cummins
TECHNICAL CONSIDERATIONS
GENERAL
SKID CONCEPT
The concept is divided into 2 skids to allow for mobility and stability.
Skids have method of manual levelling or support (e.g. manual outrigger arms).
Skids are able to be moved easily by a bulldozer (12t) or excavator (20t) without damage to the equipment.
Connections between the skids are easily disconnected and reconnected and able to fold out of way, similar to truck towing connections.
No hydraulics as difficult to maintain and complicated.
All site connections is bolted. Standard bolt sizes. (e.g. minor connection 12mm bolts, large 20mm bolts or suitable for duty).
Low wear skid plates on base of skids.
All first assembly after shipping is bolted connections if possible (limit site welding).
16hr Fuel capacity for all Diesel powered equipment.
SKID CONNECTIONS
Electrical Flexible connection points between skids are to be waterproof: IP65 ratings.
Piping connection points to highly durable ‘quick’ connections (e.g. no bolted connection points) – example is a ‘cam lock’ connection.
Connection points are to be clear of likely strike zones or protected from accidental damage.
Connection points to not be below 0.5m so as not to be too close to the mud.
Preference for fixed fluid medium pipes to be steel and fixed on each individual skid. Any direction changes are to be largest radius possible to have least impact from abrasion wear. Connections and areas that require flexibility can be flexible hose (e.g. ‘mine hose’).
Skids may be connected together for dual towing or fixing device / drawbar be removed for individual skid towing
To be capable of being towed both forwards and backwards.
SAFETY
The plant are safe to operate by a small team of operators.
Safe access to places that need operators (including platforms & handrails).
Emergency stops for all major equipment.
SECURITY
All Gold product must be protected from theft:
Sluice boxes – covers
ELECTRICAL
All electrical equipment to be IP65 minimum rating.
All equipment to have own Local control on off control.
Each skid is to have a main isolation/ electrical board. This will have one lockable isolator for all electrical equipment on that skid.
All major equipment to have individual Emergency stop buttons.
Electrical motors are good quality supplied by Huali Motors.
Power cable are supplied for Skid 2 to Skid 1, 20m long with termination suitable for Skid 1 control panel.
30% spare capacity in all power generation and physical board space
Electrical Flexible connection points between skids are to be waterproof (IP65).
LIGHTING
Each skid is to have area lighting for night works. With best light focused around areas where workers will be stationed
PAINT
Minimum of shot blast, then base coat then 2 top coats of Paint suitable for tropical, high rainfall area.
FEED BIN & FEED CONVEYOR
To be installed with Grizzly screen bars – grizzly spacing to be determined by maximum particle size accepted by trommel.
Grizzly bars to be able to protect from 250mm rocks falling 1m
Grizzly bars to be sloped to 1 side to allow oversize material to discharge off side of bin.
Feed conveyor head pulley to be cleaned by high pressure spray bar mounted on Trommel Bin.
Bin size to accept 1.5 cubic metre buckets from excavator, approximately 2-3 bucket fulls
TROMMEL
100-140 cubic metres per hour, scrubber/trommel, single screen (12mm aperture), small feed bin.
Trommel to be suitable for wet weather conditions and ensure all electrical and mechanical equipment is waterproof.
Trommel design life is 5 years, trommel screen life is 1 year.
Trommel to have:
front section as scrubber with lifters and high pressure water sprays
rear section as 12mm screen with high pressure water sprays
overflow to reject conveyor
Screen material to be bar or wedge wire suitable for heavy duty screening of wet gravel
Trommel screen to be protected from large rocks by wear bars running above main screen and along axis of trommel
Integrated skid design with Sluices and other equipment (generator, pumps pipes ect)
Feed from Trommel to Reject CV should capture nuggets (Nugget Trap)
Water injection pipes and removable plugs must be installed in and out of the screens to help with cleaning.
Advise option of a trommel spray booster pump to get high pressure sprays.
Common size bearings are to be used as much as possible.
REJECT CONVEYOR
Mounted onto trommel skid 2.
Fed via trommel oversize flow.
No support or legs off skid, can be cantilevered off skid frame if required.
Conveyor can be manually raised or lowered up to 40degrees angle from horizontal (or designer recommendation)
SLUICES
Sluices need to be in sections so that they can be dismantled and moved quickly (2m length maximum).
Sluices need to be covered in expanded mesh to stop people stealing gold. Mesh should be in form of a cover that can be locked with padlock and lifted on and off by hand.
Feed from Trommel to Sluice should go into nugget ‘trap’ box first then over sluice. Nugget box should be U–shaped with central divider that can be raised or lowered to change fluid flow. Feed from top of 1 side of U, discharge from other side of U.
Sluices to include gold mats in 2m sections suitable for -12mm product.洗
Sluices to be as wide as practical within constraints of layout.
DIESEL GENERATOR
Cummins Generator SEt
Minimum 16hr Fuel capacity for all Diesel motors
Provide 2 outlets for three phase 240V – 50Hz 15A Australian type.
Provide 2 outlets for single phase 240V –50Hz 15A. Australian type.
PUMPS
GENERAL
RAW AND CLARIFIED WATER PUMPS
24hr/7day use with provision for 1 x 6hr standard maintenance window per week
Engine brand to be used for pricing (substitutes can be recommended):
Series Diesel Engine
Model K4100D
Power 30.1 kW
Speed 1,500 rpm
Pump brand to be used (substitutes can be recommended):
Type – IS 150-125 315
Flowrate– 240m3/h
Head – 29m
Inlet 150mm / Discharge 125mm
Pump Duty:
29m head
240m3/h
200m line length
Confirm Feed rate and pressure above to be consistent with required duty of process plant pumping requirements and line type.
Raw water and clarified water pumps to be Diesel engine driven.
All pumps on skids with integrated fuel tank for easy transport and movement on site. Lifting points so can be lifted in and out of position.
16hr Fuel capacity for all Diesel motors preferred.
Raw water and clarified water pumps are capable of feeding plant enough water individually.
Other pumps on Skids to be Electric motor drive. Power supplied by Skid Generator.
Cam lock fittings or similar for suction and discharge points.
Supply of pipe by others.
PIPING GENERAL
All piping on individual skids may be a mix of fixed and flexible piping.
FILTRATION
Raw water filtration to be fitted to the skid at inlet point. ( provide 2 inlet points on both sides of the trommel skid but only 1 filter).
Filter / strainer to be self cleaning by means of manual valve operation with bypass (particle size to be determined by spray nozzle size).
Water may be fed from clarified water dams (e.g. settled tailings) or direct from River
MAINTENANCE
Designers are to take into consideration how each piece of equipment is to be maintained and make sure the design allows for easy access to undertake this maintenance.
Examples include:
Inspection and replacement of trommel bearings;
Unbogging concentrator feed or discharge lines in event of power or pump failure;
Inspection of diesel engines including removing covers;
Cleanout of clogged/blinded screens.
Low wear materials for slurry medium pipes / high velocity abrasive areas (e.g. pipe from Trommel sump to Concentrator distributor box).
Supplier is to recommend a spare parts list for all items supplied. Owner will select what spare parts are to be supplied with plant.